Part III: How Do You Bring A Virtual Cat Into The Real World?
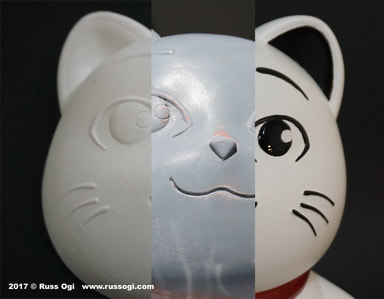
Once the changes to the virtual model were completed and approved, a 3D printed version of the model was made using a process called Fused Filament Fabrication (FFF).
For those unfamiliar with 3D printing, the software for the 3D printer takes the virtual model and divides it into layers. Depending on the part, this could be hundreds, even thousands of layers.
The layer data is sent to the 3D printer where the machine recreates each digital layer as an outline in plastic. It does this using a plastic filament that is heated and fed through an extruder. Each physical layer is stacked one on top the other.
Each layer is hot enough to adhere to the layer before it. With all the layers stacked on one another the result is a 3D physical replica of the computer sculpture.

Because the Cat has multiple colors, the different colored parts either need to be painted separately, parts need to be masked or different colors are hand painted.
When parts of a model are supposed to be separate objects, I often prefer creating the parts separately. The Cat's medallion is a great example.
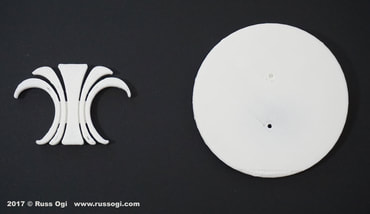
But if everything was one piece, to paint the medallion blue would have meant masking the Cat and logo in order to paint the blue or would have required careful brush painting by hand.
I often spray paint rather than brush as it's quicker and you don't have concerns about brush strokes in the finish. But doing so usually requires masking with finishes that have multiple colors.
Printing separate parts is one of the construction strategies I use to make fabrication easier. Often, this adds extra time in the CAD modeling stage of the project but can save considerable effort on the physical finishing side. Also, the finished product looks better and generally feels higher in quality.
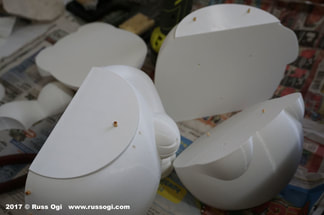
To ensure each section lines up as accurately as possible in the real world, I create alignment points in the computer model. The alignment points are pits that I fit small dowels into. In this case, I use BBQ skewers.
The alignment points are 3D printed as part of the model. In the picture to the left, you can see the alignment points some of which have the wooden dowels in them.
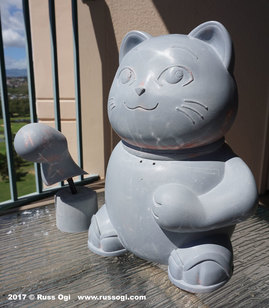
I then attach the assembled head to the assembled body. I leave the raised arm, the medallion and logo separate until later.
After the initial assembly, I give the sections a rough sand to reduce the printlines. Then, I use a filler to even out the surface. It's the same basic process that auto body shops use.
Once the model feels smooth, I do a primer coat of paint. The primer generally helps the paint adhere to the plastic and depending on the 3D print material, helps to seal the surface of the model. The image to the left shows the first coat of primer.
This first coat of primer also helps to show any places on the model's surface that needs more attention.
When I am satisfied with the model's surface, I apply a final primer coat. The Cat then gets an undercoat of black. At this point, I attach the head and right arm so I can blend the seams for those parts before the final paint goes on.
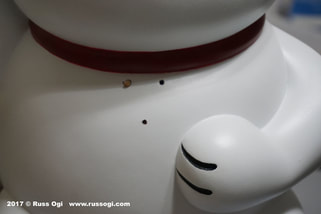
Each technique offers different benefits and limitations. I find that the situation usually dictates which technique I use.
I chose to brush paint the collar since the painted edges were well defined and getting the tape under the raised arm would be difficult. I also chose to hand paint the paws and slippers for similar reasons.
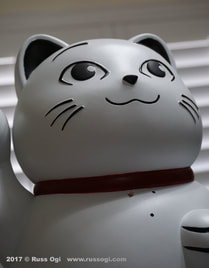
The pupils were a bit tricky. To get the shiny look of eyeballs, I opted to apply a gloss coat of clear nail polish over the black and white paint. The self leveling and quick drying nature of nail polish was perfect for the eyes.
The picture on the left shows the Cat's eyes prior to the gloss coat.
With that, the Island Cat was done. Thanks for following along. Please share any painting or fabrication techniques you use in the comments below.